手机、笔记本电脑、充电宝……这些我们每天离不开的便携式电子设备,都依赖于锂电池提供能量。锂电池的安全性直接决定了这些设备是提升生活便利性还是带来潜在风险。锂电池安全事故或召回事件时有发生,其核心关键往往在于电芯。那么,如何为这一关键部件保驾护航呢?
今天,我们就来拆解锂电芯的安全密码!
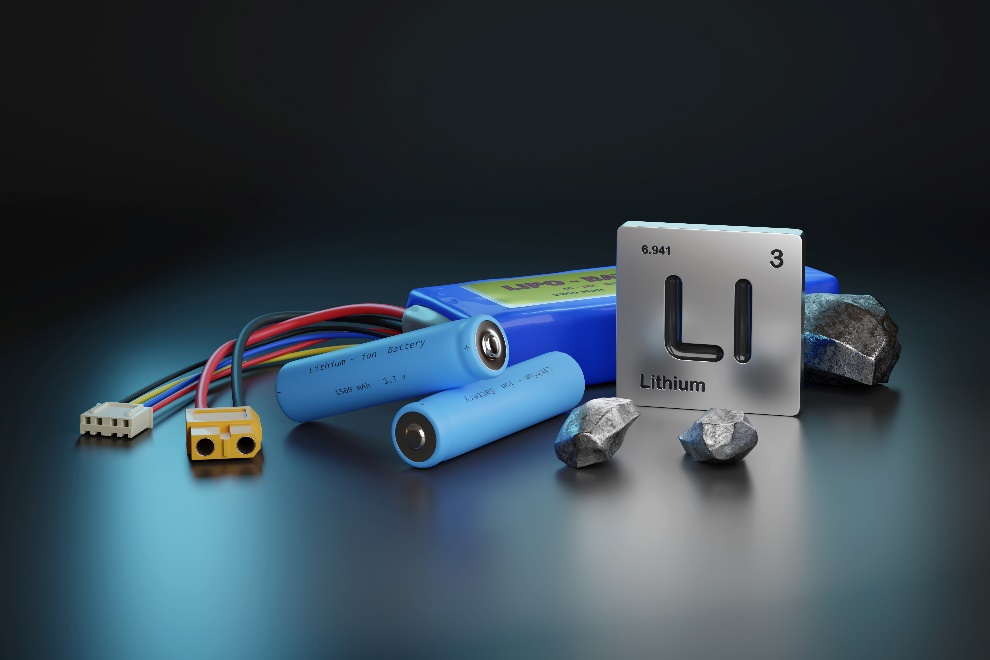
电芯为何是核心?
锂电池一般由锂电芯、保护板、连接器等组成,其中锂电芯作为电池中的能量来源和载体,是锂电池安全的核心因素。
电芯的安全性主要由以下几个方面决定:电化学材料体系、电芯设计、生产制造、检验检测,以及消费者使用条件和环境。除了消费者使用条件和环境外,其它方面均在电芯工厂内部完成。
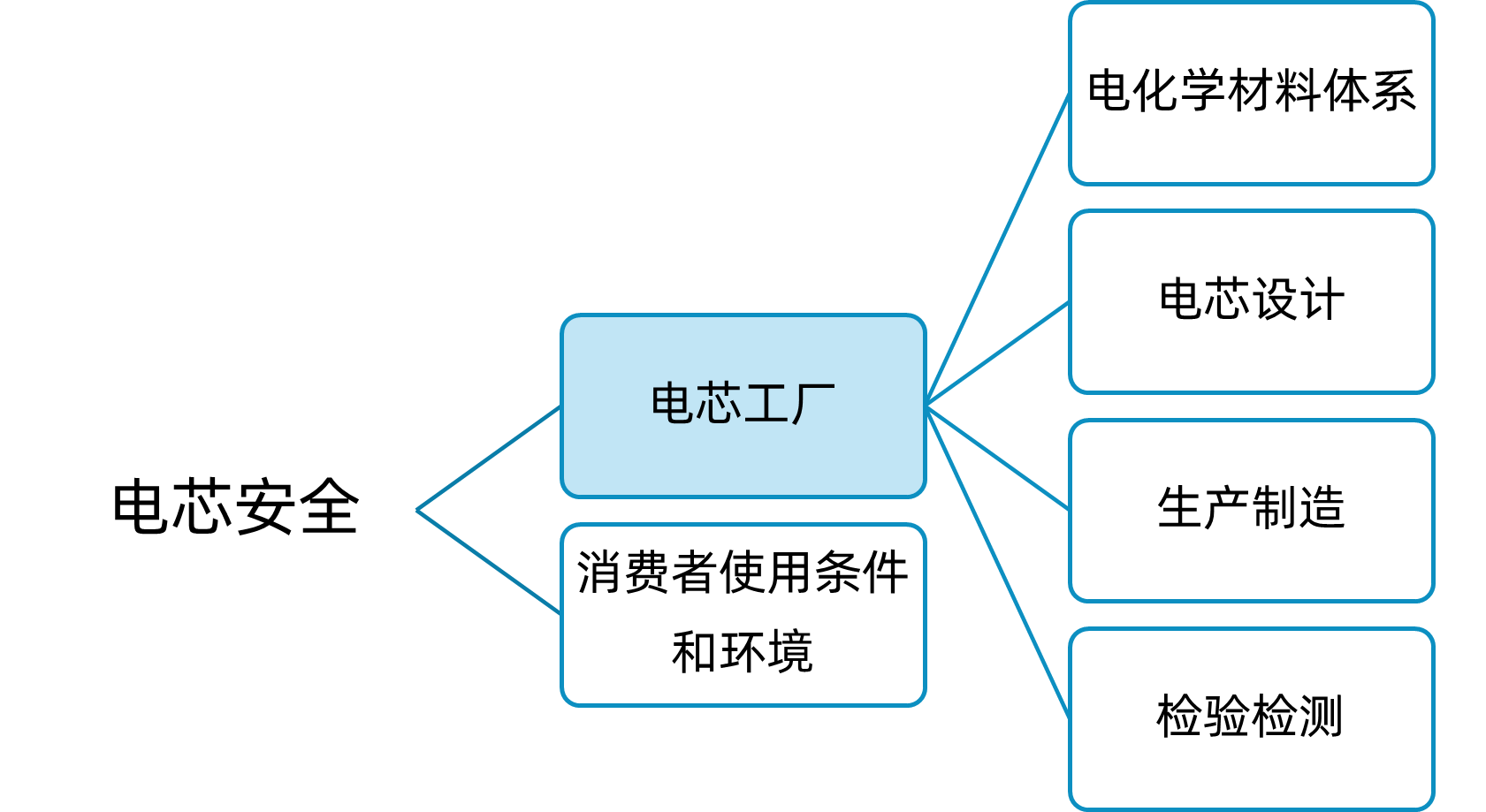
01
电化学材料体系:安全的第一道防线
电芯内部就像一座微型化工厂。选什么材料,直接决定了这座"工厂"的稳定性和抗风险能力。
锂电芯的制造需要使用多种材料,其中最主要的四种材料是正极、负极、隔膜和电解液。正极材料通常包括钴酸锂、三元材料和磷酸铁锂等;负极材料则常用石墨、钛酸锂和硅碳等。此外,正负极材料的辅材如集流体、粘结剂和导电剂,以及电解液中的锂盐和溶剂、隔膜等也都是重要的组成部分。每种材料根据自身的特性和不同需求有非常多的类型和不同厂家。
每种材料类型的变化都会影响整个电芯的电性能和安全性能。因此,在导入新材料体系或变更材料之前,进行可靠性评估和验证是保证电芯安全性必不可少的步骤。
02
电芯设计:构筑安全“骨架”
好的设计,是安全的基础。
电芯设计需要根据设备需求(尺寸、使用环境、电参数),选择合适的电化学材料体系,并设计对应的极片、隔膜和极耳等内部结构。关键参数包括正负极活性材料的配比、隔膜厚度的选择、极片压实度,以及正负极片和隔膜在宽度和长度方向上的预留比,绝缘胶带的选用和分布等。
在试产前进行设计可靠性验证是非常重要的环节,以确保电芯的安全和性能。
03
生产制造:精密制造无小事
从原材料到成品电芯,要经历50-60道精密工序。这就像一条环环相扣的安全流水线,任何一环的疏忽都可能埋下隐患。
因此,电芯工厂需要具备一定的技术水平和质量管理能力,并持续优化改进。同时,生产环境、生产设备以及各种软件追溯系统等软硬件设施也会显著影响每个工序的工程能力和管控结果,从而影响成品电芯的失效概率。
例如,生产车间的杂质控制、正负极材料涂布的稳定性、不合格极片的智能识别和移除、最大化减少极片毛刺、卷绕的一致性控制,以及减少、识别、挑出潜在内部短路电芯,电芯容量、内阻、自放电速率参数一致性匹配控制等都非常依赖智能化的自动制造、环境控制和产线检测设备,以及生产过程的质量控制。
04
检验检测:电芯出厂前的"终极大考"
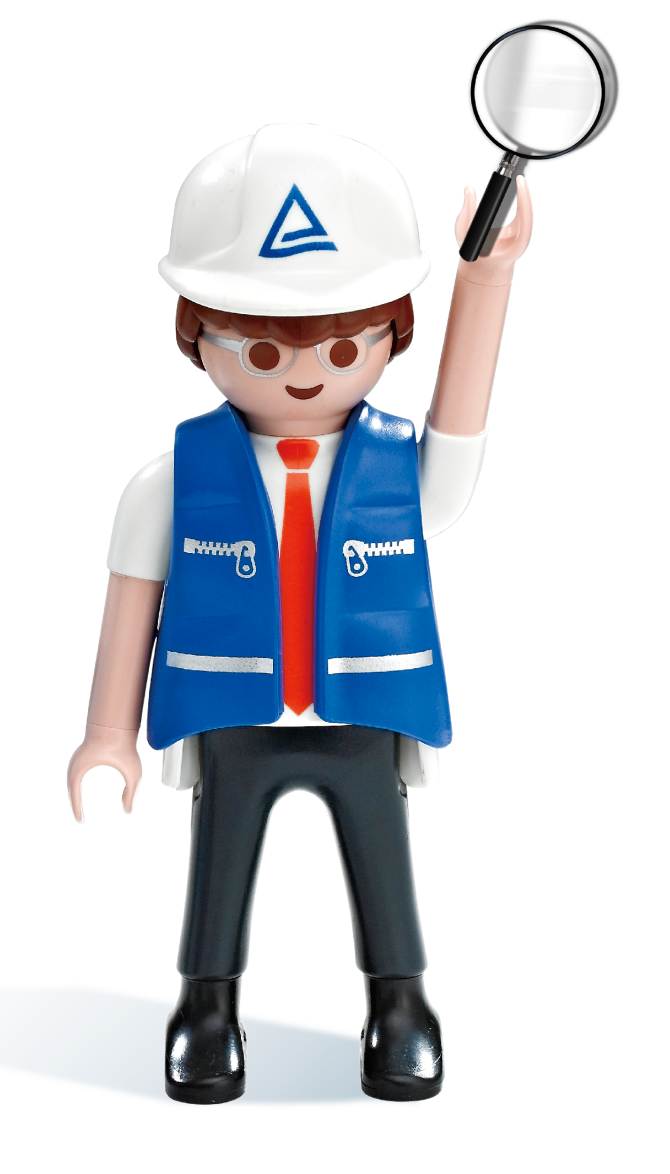
再好的设计和生产,也需要严苛的检测来验证。
为了保证材料体系的稳定性以及试产和量产电芯的符合性,电芯工厂需要对原材料、试产电芯和量产电芯进行全面的测试。建立完备的关键原材料检测实验室和成品电芯检测实验室,并编写和执行一套完整的测试标准和周期性抽样检测方案,这些都是保证电芯可靠性的重要措施。
您是否遇到过以下问题?
担心质量风险?
需要专业的第三方确保核心部件(电芯)的安全与可靠性,降低召回和事故风险。
出海遇阻?
需要应对各国复杂的认证要求,确保产品顺利进入全球市场。
供应商管理难?
缺乏足够的技术能力和资源去深度审核电芯供应商的生产体系和质量管控。
品牌信任度低?
面对激烈的市场竞争,需要权威背书提升产品信誉和消费者信心。
TÜV莱茵:守护锂电芯安全
TÜV莱茵在锂电池、电芯和充电宝等产品检测和认证领域深耕多年,得到了行业的广泛认可。依托一批在电池研发、检测领域拥有丰富背景经验的技术专家,TÜV莱茵可为电池电芯上下游产业链的客户提供检测认证和全球市场准入服务。我们能够帮助电芯企业持续提升品质控制能力,同时协助下游电池和终端产品客户提升对核心上游供应商的筛选和评价,确保电芯的安全和可靠性能。
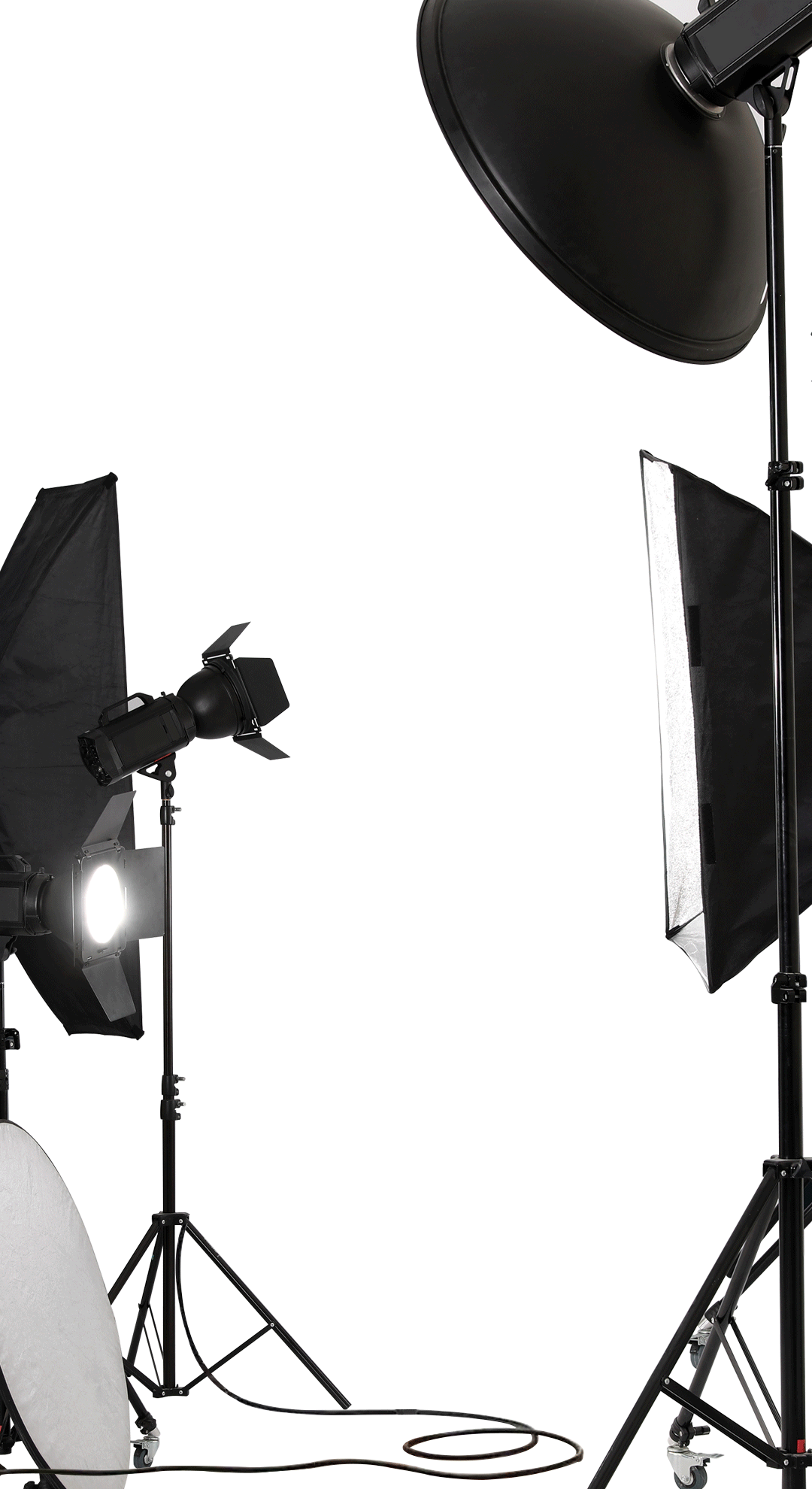